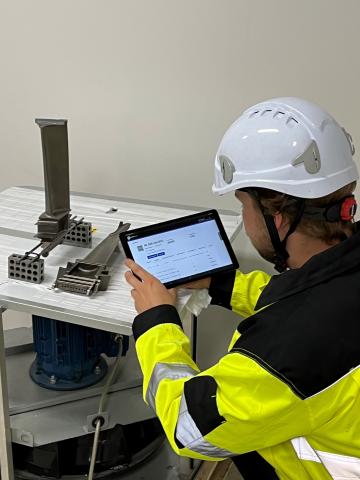
In early June, we found ourselves at one of our TMMonitor customers' sites amidst an HGPI outage. As we assessed the situation, we delved into the uninstalled components, reviewing them for the upcoming repairs. Meanwhile, the components ready to be installed awaited their final check.
Upon arrival, we wasted no time. With a tablet in hand and a smartphone at the ready, we swiftly opened TMMonitor. Serial numbers and recent repair reports of the components destined for installation awaited our confirmation. With the power of technology, we seamlessly accessed TMMonitor, effortlessly assessing the recent repair reports and serial numbers of the components yet to be installed.
We also consulted the software to review the possible repair scope for uninstalled components—whether it could be heavy, medium, or light repair. TMMonitor proved invaluable as we cross-referenced serial numbers, explored part histories, and even confirmed calculated FFH/FFS (done by TMMonitor), all while delving into past repair reports to uncover any noteworthy findings.
The efficiency and time savings offered by TMMonitor were extraordinary. No longer were we forced to go through paperwork or the need to scour customer databases for old repair reports. Instead, all the essential information resided in one convenient location, easily accessible through our trusty mobile devices or laptops. And remember, this is just one of the many exceptional features that TMMonitor has to offer!